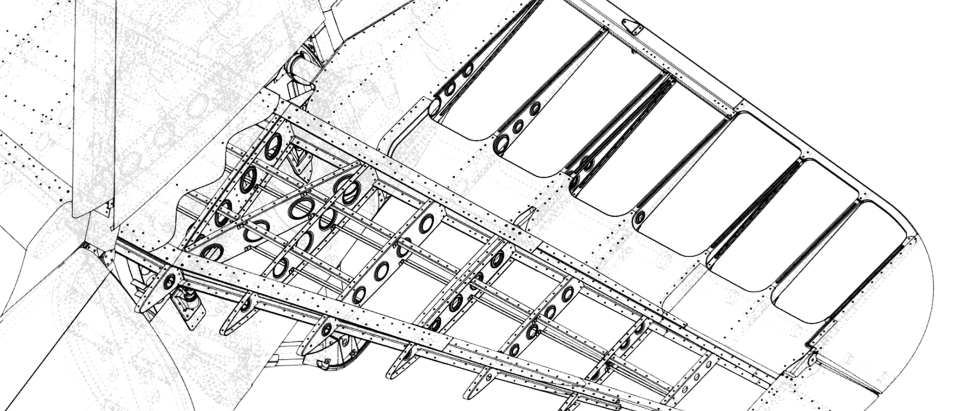
The IAR 80 airplanes were carelessly scrapped, the factory disappeared, the documentation got scattered, and the people who built or flew them gradually left us. Memories and legends remained, weathered photographs, war-scented videos, a great emptiness and a great regret. But the ’80’ did not cease to exist in the souls of Romanians. Over time, there has not been a generation that has not dreamed of building an IAR 80 again.
Achieving a 1: 1 scale replica of the IAR 80 aircraft in flight conditions is possible only through the sustained effort of a team of enthusiastic specialists with good knowledge in design, manufacturing, testing, maintenance and flight. The whole project is designed on a voluntary basis, but for the realization of the plane sponsorship is needed to contribute to purchase of materials and the costs of design, testing and operation.
1. Project objectives:
-
Construction of an aircraft that flies in maximum safety and that meets the certification requirements for the class of historic aircraft;
-
To respect as much as possible the original plans;
-
Be sustainable in terms of maintenance.
2. Design:
The documentation activity carried out during 3 years led to the identification of almost 200 original assembly drawings, most of them of structure, of the maintenance manual, of the flight manual, of the illustrated catalog with spare parts, etc. Some of them are available in the “Documentation” section of the site. For study and documentation there are several original pieces: a horizontal tail, fragments of side members, train, etc.
Naturally the next step was “learning the plane” and defining a possible configuration by selecting equipment available on the market: engine, propeller, landing gear, installations. The elaboration of the specifications for IAR 80 R was done on the following principles:
-
A structure as close as possible to the original structure of the aircraft will be made;
-
The engine variant proposed is Pratt & Whitney R 1830 with Hamilton propeller (variants used on DC 3, B 24), still available on the market, FAA certified after RK;
-
A landing gear will be adapted from a T 28 Trojan aircraft (preliminary proposal), available with FAA certificate;
-
Only new or repaired FAA-certified equipment will be used for installations that are as similar as possible to the original ones. FAA certification is required for equipment imported from the United States, where there is the largest supply for this part category.
Following these preliminary studies, a program of activities and an estimated budget were drawn up. The current preliminary calculations show that it takes about 22,000 hours of CAD design and 2,000 hours of preparation of manufacturing preparation documentation, manuals, measurement sheets, nomenclatures, instructions, etc. In total, around 3,000 drawings will have to be made.
3. Production:
The costs of design and manufacturing preparation are normally distributed over a large number of copies produced. Within this project, the realization of probably a single copy was taken into account, reason for which inexpensive constructive solutions were sought.
The main activities of the manufacturing stage are:
-
Execution of SDV for the manufacture of primary parts, mainly CNC-machined blocks;
-
Execution of primary sheet metal parts for the structure, most of which are made by cutting, forming on blocks, stretching, abkant. It requires heat treatments, surface coatings, generally specialized and expensive equipment, found only in the endowment of companies that produce elements of aviation structures;
-
Manufacture of CNC milled parts;
-
Execution of SDV necessary for the assembly of the structure – jigs;
-
General assembly of the main structural elements;
-
Installation of equipment and components for installations;
-
Checks, samples and ground tests.
Proposed approach to minimize manufacturing costs:
-
The plane will be assembled in its own workshop (~ 350 m2), in order to avoid the high indirect costs specific to large companies;
-
Parts that require specific processes: CNC milling and cutting, rubber mat pressing, abkant forming, stretching, heat treatment, NDT, surface coatings, welding, will be performed in collaboration with specialized companies;
-
For the execution of the blocks for primary parts (approximately 600), CNC machined MDF will be used. Tests already performed for pressing sheet metal ribs on rubber mat press have demonstrated feasibility for small series;
-
The gauges for assembling the structure will be manufactured in our own workshop;
-
The assembly of the main structural elements, the junction, the general assembly, the tests and the measurements will be performed in our own workshop.
The estimated budget for manufacturing includes a need of ~ 15000 direct labor hours for the assembly of the structure and installations, plus mainly CNC hours. The remaining processes that require lower costs will be determined as the execution drawings are made.
4. The main phases of the project:
-
Completion of all documentation in CAD system (see Planning);
-
Manufacture of a horizontal tail: blocks, primary parts, gauge, assembly;
-
Elaboration of the final budget based on the costs registered at the production of the tail;
-
Obtaining the necessary sponsorships for the complete manufacture;
-
Manufacture of complete aircraft;
-
Certification, ground and in-flight testing;
5. Conclusions:
-
The project is feasible. The aircraft can be made from the original existing documentation;
-
It is a laborious project, which requires a large volume of design and manufacturing work:
-
24000 design hours,
-
15000 direct labor hours,
-
a number of machine hours for specialized operations, which will be determined as the project is completed.
-
-
The project can be realized by engaging as many experienced specialists as possible;